I had a Holden Commodore 6-cylinder shroud lying around, so it became the test mule to see what was/wasn't achievable. The shroud was clamped to the workbench and the kids' mini skateboard used as a moulding tool.
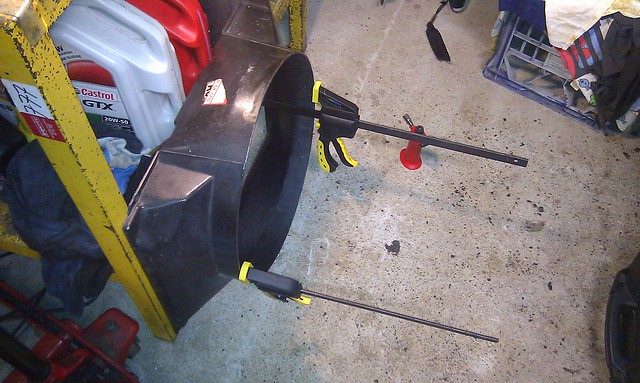
A butane torch was the heat source and - after a bit of trial and error - I got a bit of a technique down on how to heat and mould the plastic.
The test also showed it was easier to clamp the skateboard to the workbench and bring the shroud to the modifying wheel like so...
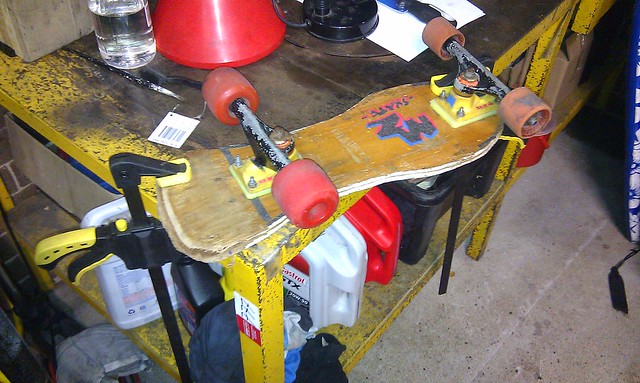
If I was to do it again, I would have had a 2nd person heat while I worked the shroud over the skateboard wheel as it was hard to heat, then quickly work the softened plastic.
But, I got there!
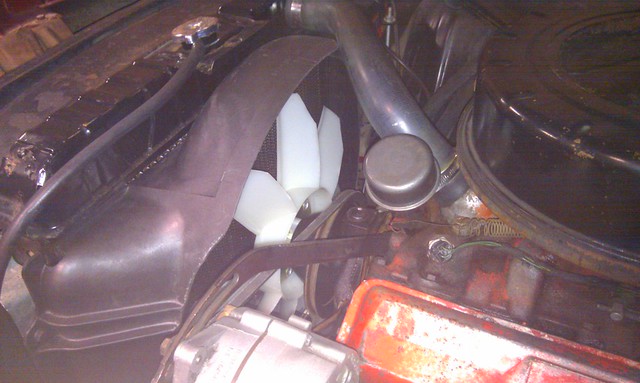
The fan sits low in the shroud, so there is a larger gap a the top than the base, but it should be an improvement over no shroud at all.
No comments:
Post a Comment