Originally the plan was to try and bend/twist the inlet pipe but too hard in the end.
Plan-B: source a new inlet pipe.
The KYB make of power steering pumps have an inlet that pushes into an o-ring and is held in place by a keeper plate. From various photos throughout the web, it looked like KYB standardised on the pipe diameter/keeper plate arrangement and simply changed the direction the pipe was bent to suit the vehicle it was going into.
After a bit of a dig through photos and visiting the wrecker near work with a set of verniers, I went for a second hand Hyundai unit from eBay.
The inlet pipe was duly unbolted and - thanks goodness - has an identical mounting arrangement to the Commodore's!
It was soon bolted to the Commodore pump and dummy-fitted to the ancillary drive bracket...
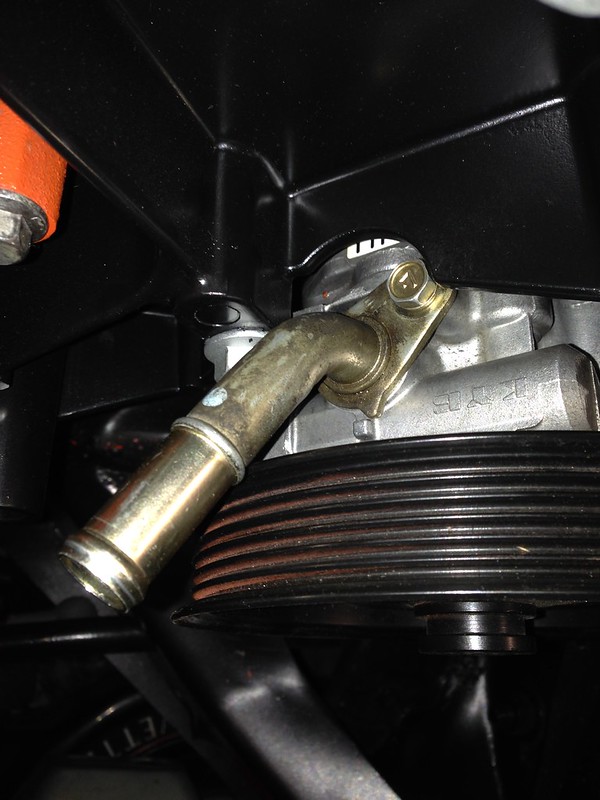
So the orientation of the inlet is MUCH better. You can see in the photo that the relief in the bracket sits hard against the keeper plate bolt. The angle grinder came out and five millimeters was quickly removed.
Went ahead and bolted the alternator, idler pulley and tensioner into place. Juuust managed to get the Commodore drive belt on (need to get a longer one) with the tensioner at the extremity of its travel...
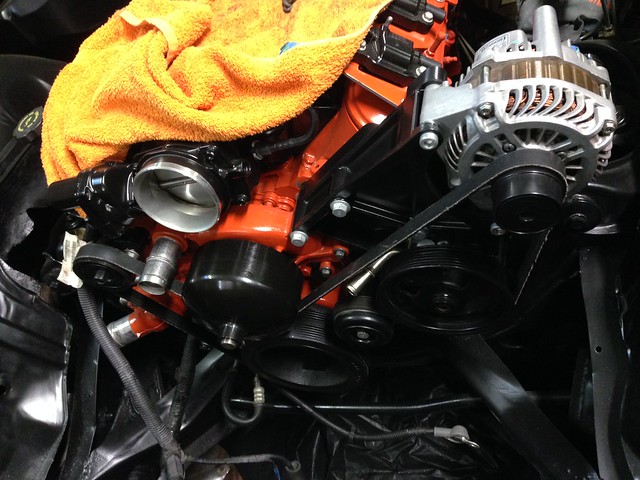
Evident in the photo above, the power steering pump inlet peeks out between the belt and the power steering pump pulley.
It is all a bit tight for my liking so time for Plan-C, enter one Mitsubishi Lancer power steering pump...
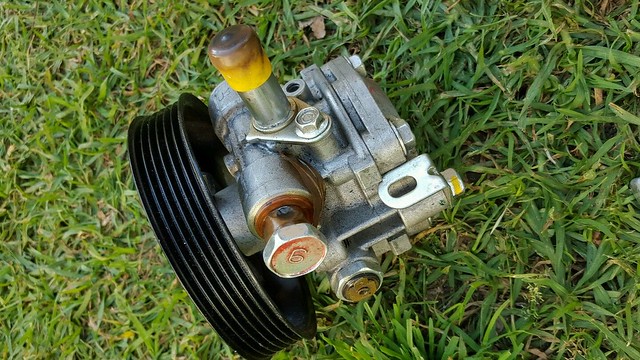
Here the inlet is vertical into the pump, so no belt clearance issues (I hope!).
I pick it up next week, stay tuned.
J